Automated Guided Vehicles: The 5 Main Things To Know
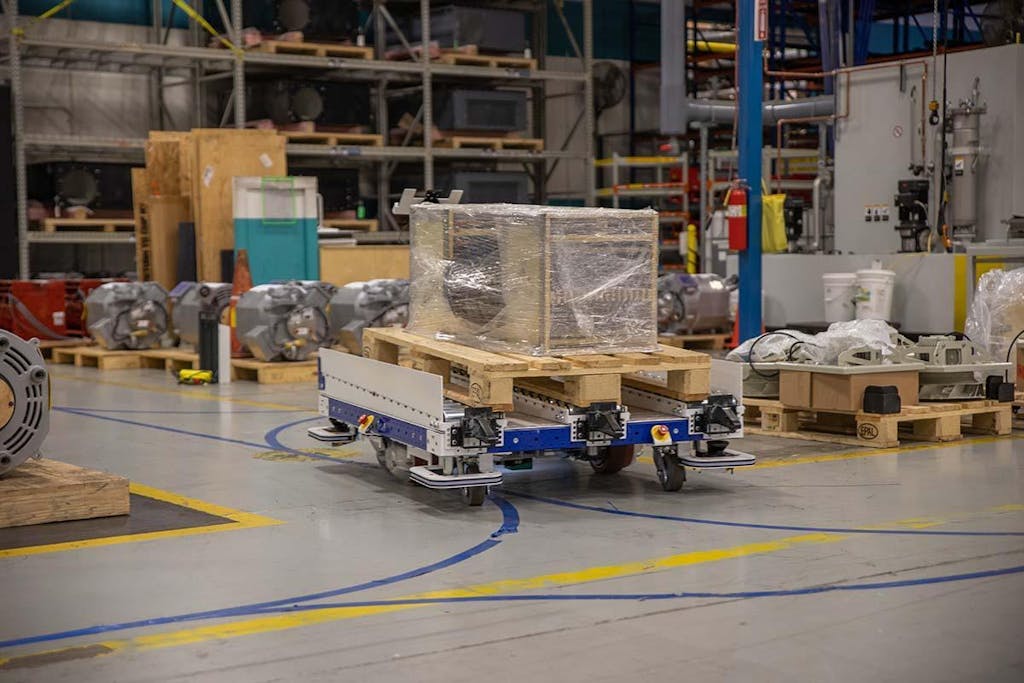
Last Modified: 29.08.2022
AGV, or Automated Guided Vehicles, with its self-driving solution for material handling is catching the attention of managers in all sectors. This is not shocking news since a more high quality navigation system, safety protection and autonomous efficiency of material handling can be implemented in the operations leading to long-term operational and ROI advantages. According to Research and Markets, the aggregated sales of automated guided vehicles crossed $3 billion in 2021 alone!
This article discusses:
- What AGVs are?
- How AGVs work?
- Everything else you need to know before buying and implementing them in your facility
If you want to know more about the AGV solutions provided by FlexQube, click here!
What is an automated guided vehicle system?
An automated guided vehicle is a driverless electric vehicle used to transport materials within a plant, distribution center, warehouse, or factory. You can program its path and destination with the option of a collision warning. The seed for AGVs started budding in the 1950s. By the late 20th century, the technology was evolved enough to make AGVs practical.
Today, AGVs offer advantages in the field of logistics systems by handling material flows automatically.
The AGV robot needs to cover some basic requirements before it can be considered an AGV:
Self Driving: AGV by definition needs to be self-driving. This means that there shouldn’t be any operators involved in the driving or transportation of material with AGVs.
Collision Warning: There also needs to be some sort of collision warning, before the vehicle can be classified as an AGV. This means that the AGV has to be ‘smart’. It should have hardware and software to both detect collisions and avoid them.
Navigation: An AGV needs to have some sort of navigation technology. In other words, it needs to be able to navigate through the facility on its own.
Path: AGVs should be able to follow paths set by operators. They should also have the capability to choose the destination they are transporting goods to.
AGVs are guided by specific pathways within the facility in which they operate.
AGV using a magnetic tape for navigation
These pathways are defined by magnets, wires, radio waves, or visual markers. AGVs identify these paths with lasers, magnets, RF sensors, optical sensors, or camera vision systems.
The advantages of using automated guided vehicle systems
Implementing AGV robots in your facility offers many advantages over standard material transport options like forklifts or human labor. We list the key benefits below:
Error elimination: Nearly a quarter of unplanned downtime in factories is caused by human errors. Automated guided vehicles eliminate human errors in material handling.
Increased safety: AGV robots can significantly improve material handling safety within the facility. They have hardware and software safeguards to protect staff and materials, even while moving heavy loads.
Lower labor cost: According to industry estimates, there is a shortage of nearly half a million employees in the warehousing industry alone. AGVs help to reduce labor costs as your employees have to do less work. They also assist workers to perform their tasks at a faster pace.
Accuracy: AGVs move materials with very high accuracy. Even in a limited space, they can be designed and programmed to work with those constraints.
Productivity: As a culmination of reducing errors and delivering materials accurately, material handling efficiency significantly increases. AGVs increase the productivity of the whole plant operation, not just material handling.
On top of everything mentioned above, AGVs can help you optimize material handling and transportation by ensuring just-in-time deliveries and avoiding overstocking. This is called milk-run logistics and is regularly applied to optimize a supply chain.
Industries that use automated guided vehicles
The core functionality of an AGV robot is to transport materials from point A to point B. They can be used in any industry that requires material movement – which is most of them.
There is no question that organizations are moving towards warehouse automation and agile manufacturing. As implementation costs continue to drop, AGVs are poised to see even wider adoption.
Even though their initial and primary usage was in manufacturing, warehousing, and distribution centers, the pandemic has accelerated the application of this technology in many other industries like:
- Food & beverages
- Healthcare
- Agriculture
- Retail
- Indoor and Outdoor Deliveries
- Cleaning
- Pharmaceutical industry
It was really interesting to see industries that require hygienic and sterile environments rely on AGVs to help reduce the chances of contamination.
Despite their benefits and advantages, Fortune Business Insights reports that the high initial costs of implementing automated guided vehicle systems are still a challenge for some businesses.
However, many companies are still going forward, especially in North America where the AGV market size is predicted to grow at full tilt:
Now, let’s see if your facility is ready for an AGV system.
5 things to consider before buying an AGV robot
If you are thinking about AGV implementation within your facility, there are some important things you need to consider. Continue reading to find out more, so you can make an informed decision.
1. Should you automate?
The primary factor to be analyzed is the need for automated material handling and the opportunity cost of not doing the same. In this phase you need to answer questions like:
- What will be the material flow path?
- What is the load to be transported?
- What will be the impact of AGVs on employees?
- Do you have a use case that demands the use of AGVs?
- What will be the break-even period for AGV robots?
These considerations will determine how to introduce AGVs into your operation and get everyone on board.
2. What type of AGV robot do you need?
There are many different types of AGVs and you should choose the right one for your needs. These are the main things you need to consider:
- the type and weight of the load to be moved
- dimensions, fragility, and stability of materials to be transported
- frequency of transportation
- the layout of your facility
- the cost of the implementation
It is important to note that there are different types of AGVs available, and they include:
Unit load AGVs: They are designed to carry a single unit of material to be transported. An example is an AGV specifically designed to transport a single roll of aluminum sheet.
Towing AGVs: They do not carry any load themselves but tow pallets or carts that contain the load. This is suitable when materials to be transported arrive in carts with wheels.
Light load AGVs: They are specifically designed to transport material for short distances. These AGV robots are used for moving goods up to 500 pounds between two processes within the same facility.
Forklift AGVs: These robots are to replace human-operated forklifts in warehouses. They can identify the pellets that need to be moved and the location where they have to be placed.
Custom AGVs: FlexQube designed the AGV – a unique, modular AGV that can be designed in different sizes based on processes, operators, materials, and facility layouts.
Lastly, you will have to consider how AGV enables the optimization of space in your warehouse. For small warehouses with limited space, custom material handling solutions are often the best option.
3. Which navigation technology is the best?
For AGVs to function optimally, they have to have a way to get around – with precision. This makes the choice of navigation technology one of the most important decisions when selecting an AGV robot.
There are a few navigation options out there, and they include:
Magnetic Tape: Magnetic tape that is laid down on the floor. AGV robots use magnetic sensors to follow the path throughout the facility.
Magnetic Spot: Similar to magnetic tape, metallic magnetic pucks are installed on the floor of the facility. Once again, the AGV is fitted with a sensor that allows it to follow the line of magnetic spots.
Inductive Guidance: With this method of guidance, a current-carrying wire is manually installed on the floor. AGV robots detect the inductance of the wire to identify the path they have to follow.
Laser Guidance: The facility area is mapped out and stored within the AGVs memory. The facility also needs to be equipped with multiple fixed reference points, and reflective strips that AGVs can detect. They use lasers to triangulate their current position and where they have to go.
GPS navigation: GPS satellites are used by AGVs to navigate along a path. GPS is usually used outdoors and has limited use across interior shop floors due to lower accuracy.
You have to understand the capabilities and constraints of your facility to decide on the guidance system to use.
For mostly outdoor operations, GPS navigation is the way to go. For precise indoor movement, inductive guidance is the best solution. If the shop floor is unlikely to be obstructed, all other options can do the job.
4. Should you upskill your workforce?
One of the prominent reasons for using AGV robots are labor shortages in inventory and logistics operations. According to industry estimates, there is a shortage of nearly half a million employees in the warehousing industry alone. AGVs can bridge the gap between available labor and labor required.
Depending on where you are right now, introducing automated vehicles on the shop floor can mean a significant change in the way your facility operates. The processes and workflows in the facility will have to be adjusted – but it is a change for the better.
First, you need to address any concerns your employees have. They might be skeptical of new technology in their workplaces and potentially scared for their jobs.
Clear any ambiguity or concerns they may have before proceeding with the AGV purchase. Showcase the potential productivity increase of the facility and how they will also benefit from AGV robots. Highlight the increased safety and reduced physical work that is possible by working alongside AGVs.
If you own some form of a guided vehicle, depending on the technology level it can be quite easy to train employees to work with new robots. Our AGV can be managed through an Android tablet system. This is beneficial for your operators as they are already familiar with such technology; however with other AGV systems they need training targeting the specifics of the new robot.
A much more extensive upskilling effort would be expected in a factory that never had any sort of automated equipment if not taking progressive steps into automation. Their staff needs to be gradually introduced to autonomous technology. They should be trained on the specifics of a new robot only after they have a firm understanding of the underlying basics. It is a wise strategy to hire workforce consultants who have experience with autonomous technology.
5. What are the ancillary technologies you use?
In the Industry 4.0 paradigm, all assets and pieces of equipment in a facility should be able to communicate with each other. The existing digital infrastructure of your facility should work well with the hardware, software, and communication layer of the new automated guided vehicles.
In an ideal world, the data from your AGV should also be compatible with the ERP and MES (manufacturing execution system) you use to manage your operations.
The next step: a custom AGV?
Some businesses will struggle with prebuilt solutions as they will not match all of their needs. If you are one of them, fret not – we have a solution for you as well.
For facilities that require custom material handling carts, FlexQube designed a AGV SYstem – a unique AGV that is designed to accommodate processes and operations in every facility, with no need to change existing infrastructure or material handling fleet.
Traditional AGVs are only available in limited sizes. FlexQube’s AGV is available in any size up to 2510 mm (98 inches).
Traditional AGVs are only available in limited sizes, whereas the AGV is available in any size up to 2510mm / 98 inches. This means that you’ll never have to compromise on your requirements: we can design a custom AGV for you, based on your processes, operators, materials, and facility.
You can start the process today by analyzing your options with a FlexQube expert technician. Tell us about your requirements and our team will help you find the right solution for your facility.