What is Just-In-Time Manufacturing?
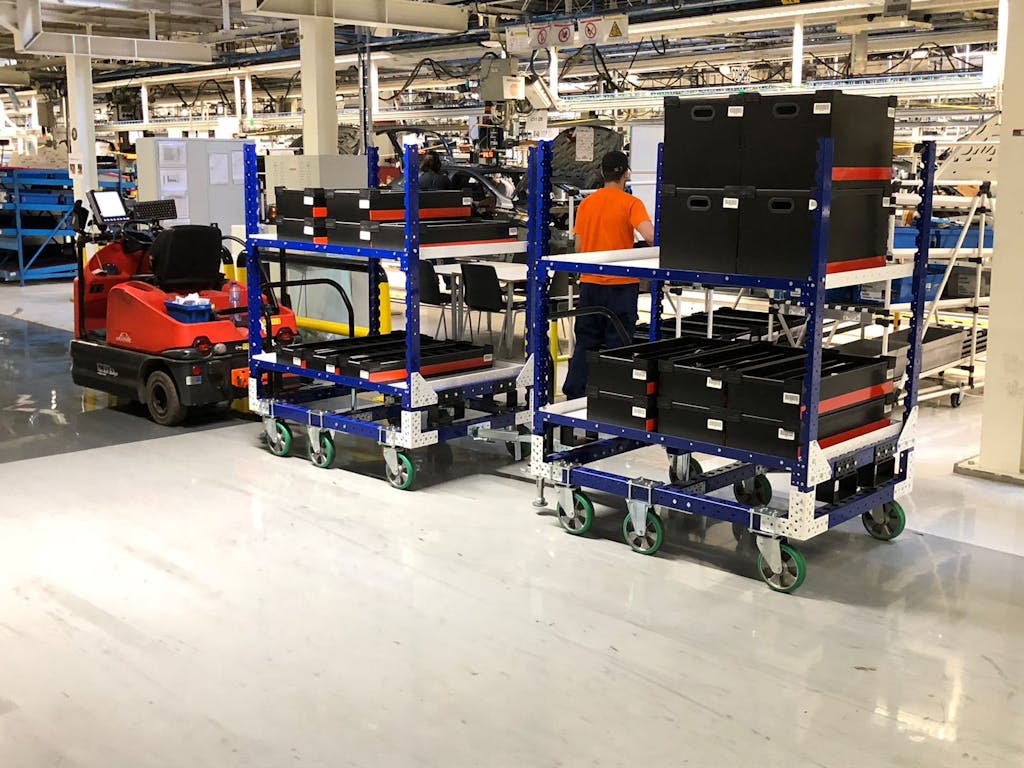
Just-In-Time Manufacturing or JIT Manufacturing, for short, was developed in Japan during Toyota’s time developing the lean manufacturing tools and models in their manufacturing.
The JIT system allows a company to start the manufacturing or the purchasing process once the customer places an order. Meaning that there is relatively zero inventory needed. Simply put, a JIT manufacturing environment has materials and goods purchased and produced when they are required.
The premise is based on providing the goods just in time, only once the order is placed by the customer. The JIT system can help to identify hidden problems in the supply chain and can lead to a reduction in production waste throughout the process. While this concept may seem simple and easy to implement, it needs a lot of coordination within the supply chain and operations to ensure no delays or setbacks throughout the production.
Different Manufacturing Methods
The JIT manufacturing method differs from the other two traditional manufacturing methods, the push and pull methods. The push method is generally is the Make to Stock form of the manufacturing system. Therefore, the production isn’t based on any demand from the customer. This method leads to a build-up in a large stock inventory and can put pressure on other areas of the organization.
The pull method, however, revolves around Make to Order form of production. This means the production is based around a customer order and is based on actual demand. Development in technology made it much easier to implement a pull system, and this type of system is how JIT manufacturing was developed.
Benefits of JIT Manufacturing
Results from implementing a JIT production process can include increased quality, productivity, and overall efficiency. Improved communication between departments and a decrease in costs and waste are also recognized benefits of the system. Because of the growing competitiveness on the global market and the value of these benefits makes the idea of implementing JIT manufacturing very tempting to many international organizations.
One of the main benefits of JIT is a considerable reduction in inventory levels. This can lead to lower costs and investments in inventory, freeing up capital for other internal projects. Because only a minimal amount of materials is needed to begin the production, it can substantially reduce the inventory levels. In many Japanese companies that use the JIT concept, they report a reduced working-capital turnover ratio.
Under the JIT manufacturing method, quality levels are also often reported by companies. Because of the smaller order quantities, issues in the quality can be identified quickly. The uncovering of these quality issues leads to a correction as soon as the problem is noticed.
Some other benefits of implementing the JIT manufacturing system include:
- reduced investments in facility space for inventory and production,
- Reduction in direct material costs,
- Less risk in inventories
Implementing JIT Manufacturing
As mentioned above, the JIT manufacturing system isn’t incredibly complicated; however, implementing and maintaining can be difficult. Issues such as changes over time, varying production schedules, and long lead times from suppliers can make this system difficult to implement. We suggest focusing on getting your workforce involved within the idea of JIT as the primary production method. Also, educating your team on making a shift towards reducing waste and developing a zero lead time mentality. With this type of buy-in from your organization, implementing JIT manufacturing can be a much smoother process.
JIT manufacturing had its beginning in Japan, during the birth of lean manufacturing. But since then, it has taken hold in many large international organizations striving for success and excellence in the competitive global market. Today JIT encompasses a full package of ideas, methods, and processes for creating a production system that can lead to significant benefits throughout the production process.