The Top 10 suggested Lean Tools.
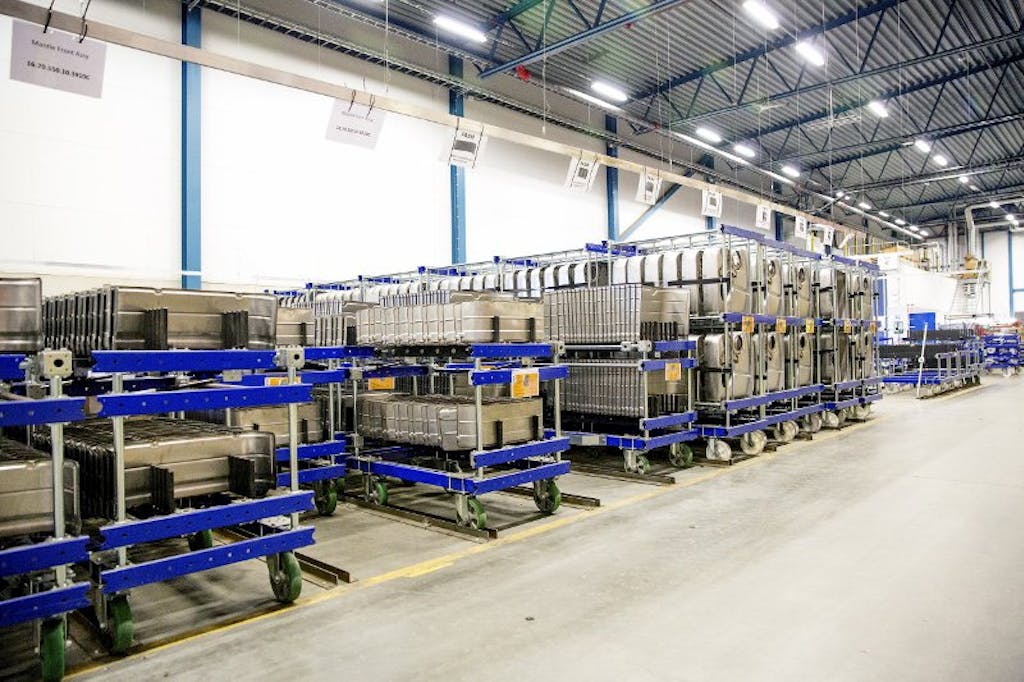
Learn about the top lean manufacturing tools. Lean manufacturing and its principles are critical guidelines for manufacturing facilities globally.
Within the principles of lean, there are specific tools that can be implemented at different times to counteract various problems. We have discussed a number of these tools in earlier blog posts, such as the PDCA cycle and Jidoka methodology. But in this post, we will provide short summaries of 10 of our suggested lean tools for you to implement. The ten tools we will summarise are:
- Poka Yoke
- Kanban
- Six Big Losses
- Takt Time
- 5S
- Root Cause Analysis
- Gemba
- SMART Goals
- Value Stream Mapping
- Bottleneck Analysis
Poka-Yoke
Poka-Yoke is all about error detection and ensuring that if there is an error, it doesn’t go on to the next phase of manufacturing. The goal of Poka Yoke is to achieve a zero-defection rate throughout the production line. It was initially coined in Japan and initially came about as fool proofing but later evolved into mistake-proofing. The benefits of Poka-Yoke lead to saving time and money by limiting the number of faulty products through to the next stage of the manufacturing line.
Kanban
Kanban means a signboard or visual board and is a card system to help organize the material flow of goods through a manufacturing facility. Kanban began in the 1940s as an easy to use planning system within the Toyota automotive. Kanban helps in visualizing the actual process of materials, and the cards can be used as a “pull system” that signals when more goods are required. This can help bottlenecks in the manufacturing line as well as help to prevent the oversupply of certain materials.
Six Big Losses
The six big losses are six different areas of productivity and efficiency loss. It’s a useful method for identifying where the significant losses come from and guidelines on how to eliminate the waste. The six big losses are:
- Unplanned stops
- Planned Stops
- Small stops or idling
- Speed or slow cycles
- Production Defects
- Startup Losses
Takt Time
Takt time can be seen as the even pace or the rate time that it takes to complete a finished product that can be delivered to a customer. It is widely referred to as the speed of production, and this tool can be very beneficial in understanding what needs to be produced each day. The Takt time can be determined by finding out the amount of available work time during the day divided by the customer demand for a particular product. For example, if there are 420 work minutes per day and the customers demand 30 finished products per day. Then the takt time is 420/30 = 14 minutes. This means that a product needs to be finished every 14 minutes to keep up with the demand.
5S
5S is a method for organizing different workspaces, so they are prepared for optimal work safety and capacity. Its primary focus is ensuring the tools, materials, and items are placed in the positions they need to be in, and the entire workspace is kept clean. The 5s systems include the following steps:
- Sort
- Set in Order
- Shine
- Standardize
- Sustain
These five necessary steps help to eliminate waste within manufacturing that can be produced from unorganized workspaces.
Root Cause Analysis
The Root Cause Analysis is a problem-solving method that is designed for finding what is behind the cause of the problem in the first place. Stopping any manufacturing process whenever an irregularity is found, then conducting an investigation is one of the best ways to complete the root cause analysis. One of the most common forms of finding the root cause of a problem is the five why approach. This involves asking why five times to reach why the problem occurred.
Gemba
Gemba is a Japanese term for the “actual place,” and this can refer to getting away from your desk and going to the “actual place.” You may use Gemba when there is a problem that needs to be solved or if you are working on an improvement project. This helps in ensuring that the problem solving or improvements that you are planning will work in reality.
SMART Goals
SMART goals are being used in a wide variety of businesses and departments now; this only goes to show the usefulness of the method. SMART stands for:
- Specific
- Measurable
- Attainable
- Relevant
- Time-Specific
This can help in planning and strategizing plans to help make goals more effective.
Value-Stream Mapping
Value stream mapping is a tool for helping to map out the flow of the production process. This is beneficial for seeing a top-down perspective of the flow of your materials in your production line. Using this tool can help you find delays in the process, inefficiencies in certain areas and improvements. An initial value stream map can also be used as a tool to outline future developments for the production and where waste can be eliminated.
Bottleneck Analysis
The Bottleneck Analysis tool is used to find areas in the process where efficiency is restrained. This helps manufacturers to find the areas that need to be focused on to improve the throughput of the manufacturing line. Improving areas where there is a bottleneck can lead to improved output in other areas of the process.
We have outlined short summaries of the ten lean tools that we think could be beneficial for your manufacturing line. If you haven’t begun with any of these yet, we would recommend starting slowly and only picking one or two that could make a significant impact on your manufacturing line. Beginning off by trying to implement all ten at the same time could have adverse long term effects, and it is better to perform one at a time.
At FlexQube we ensure that we are able to make use of lean tools as often as is applicable.