Autonomous Robots and Innovation in Intralogistics
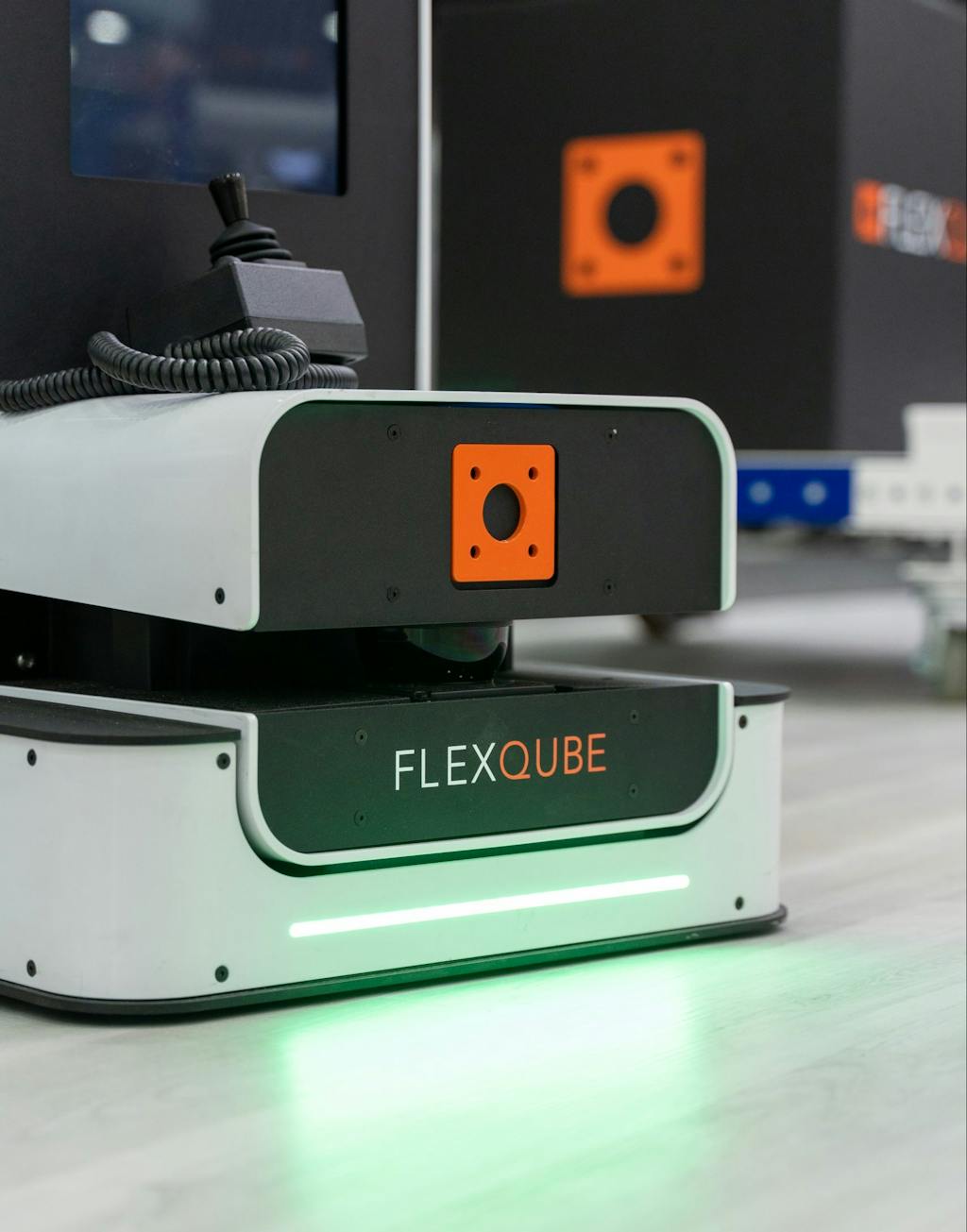
Autonomous robots, also known as AMRs, are transforming how companies handle logistics in material handling. The global market of mobile robots is forecasted to reach $72.5 billion by 2030.
By automating tasks that were previously performed by manual labor, autonomous robots bring increased efficiency, productivity, and safety to the workplace. Companies are increasingly competing to satisfy consumers’ ever-changing demands. AMR is getting increasingly recognized as an innovative and flexible solution. This solution will optimize material handling in warehouses, factories, and other operations.
With this in mind, FlexQube have implemented the latest robotic technology in the product line. These autonomous robots bring new levels of innovation to intralogistics and material handling in your current and future operations.
This article will discuss:
- Advantages and Challenges of AMRs in intralogistics
- The future of Autonomous Robots in Intralogistics
Advantages of autonomous robots
Intralogistics is a critical component of many industries. The traditional approach of humans manually moving goods can be inefficient and costly. Autonomous mobile robots (AMRs) are transforming intralogistics. They enable warehouses and other industrial facilities to move goods more quickly, safely, and cost-efficient.
AMRs are designed to automate the process of transporting goods from point A to point B. This automation enables employees to focus on more important tasks. Hence, the ability for autonomous navigation, collision avoidance, path planning and autonomous re-routing reduces the need for manual guidance. Labor is also reduced.
FlexQube offers non-load AMR products. These products can transport various carts with different sizes and loads. This increases the flexibility of operations. The robots can dock themselves to loaded carts with motorized attachments through a standard interface.
Once docked, the robots transfer power and data to the motors of the cart. This enables the cart to navigate through the facility, bringing the right materials to the right destination. Hence, AMRs (Autonomous Mobile Robots) are capable of sophisticated data collection and analysis. This allows them to navigate difficult terrain, narrow passages, and stairs, increasing their range of applications.
Furthermore, AMRs can reduce the potential for human error and workplace accidents. Autonomous robots can be used for transporting goods. They are not subject to fatigue or distractions.
Therefore, they can safely and accurately transport goods without any risk to personnel. With the ability to detect and avoid obstacles automatically, AMRs can also help ensure that goods remain undamaged while in transit.
Challenges of autonomous robots
The rise of Automated Mobile Robots (AMRs) in intralogistics is transforming how businesses manage their day-to-day operations. However, certain challenges must be addressed for businesses to take full advantage of this technology.
One of the biggest challenges is safely navigating the world around them. Autonomous robots must be able to detect and recognize objects and obstacles in their environment. They must also make decisions on how to avoid them. This requires complex algorithms and sensors that can accurately interpret the environment.
The installation of AMRs must, thus, be programmed to navigate the environment and interact with other objects safely. If not programmed correctly, robots can risk injury to people in the area. To ensure the installation is programmed correctly, managers should take advantage of any installation service provided by the manufacturing company.
Another challenge is dealing with unexpected events. Autonomous robots must be able to respond quickly and correctly to changing conditions. This requires the robots to be able to identify and analyze different situations and make decisions in real-time.
Additionally, AMRs require a significant amount of data to operate efficiently. This data must be collected and analyzed to optimize the robots’ movements, which can be a prolonged task. However, the manufacturing company typically offers training with the first installation, allowing consumers to operate the robots freely.
These challenges are difficult, but not impossible. With advances in artificial intelligence and robotics technology, it is becoming increasingly possible for autonomous robots to navigate. They can also respond and interact with the world around them.
The Future of Autonomous Robots in intralogistics
In the near future, autonomous robots will become increasingly common in intralogistics. Autonomous robots could be used to automate many tasks in warehouses, including order picking, stocking, sorting, and transportation.
Autonomous robots are expected to be increasingly adopted in intralogistics operations in the coming years. According to Statzon 2022, the global mobile robot market value is expected to reach 72.5 billion USD with a CAGR of 21% by 2030.
The reason for this growth is a direct consequence of labor shortages and increased consumer demands. This has led to an increased need to streamline production and manufacturing systems. As autonomous robots become more prevalent, intralogistics operations are expected to become increasingly automated.
The future of autonomous robots will bring innovation to intralogistics and material handling. This will provide more efficient, cost-efficient, and reliable solutions for warehouse, manufacturing, production, and other operations. Complex tasks will be managed with greater accuracy and speed by taking away the potential for human error. Materials will be transported quicker and more safely with AMR navigation, reducing the amount of time needed for material handling tasks.
Autonomous robots could, thus, be used to optimize warehouse layouts and reduce costs. They will also be used to improve safety, reduce customer wait times, and improve customer satisfaction.
Autonomus robots will be used to increase the speed and accuracy of intralogistics operations. This will reduce the need for human workers and allow companies to become more efficient and profitable. In result, these companies will become more profitable.
The future of autonomous robots will offer improved scalability and flexibility compared to traditional intralogistics solutions. This will allow for easier and faster configuration. Furthermore, AMRs have the ability to be programmed to adapt to changing conditions quickly. This will lead to maximized efficiency and minimized downtime in future intralogistics.
Key Takeways
Autonomous robots are transforming how companies handle logistics in material handling. The global market of mobile robots is forecasted to reach $72.5 billion by 2030.
Advantages of autonomous robots include increased efficiency, productivity, and safety in the workplace. Reduction of manual labor is also a benefit of autonomous robots. Automated navigation, collision avoidance, path planning, and re-routing are all capabilities of autonomous robots.
Challenges of autonomous robots include safely navigating the environment, dealing with unexpected events, and requiring a significant amount of data to operate.
The future of autonomous robots will bring innovation to intralogistics and material handling, providing more efficient, cost-efficient, and reliable solutions. It will also lead to improved scalability and flexibility, and the ability to adapt to changing conditions quickly.
Hence, AMRs transform intralogistics by increasing efficiency, reducing costs, and improving safety. Thus, automating the process of material handling is becoming an increased priority among managers. Providing a solution for flexible and optimized production processes is also receiving more attention.