What Factors into the ROI on Replacing Your Forklift?
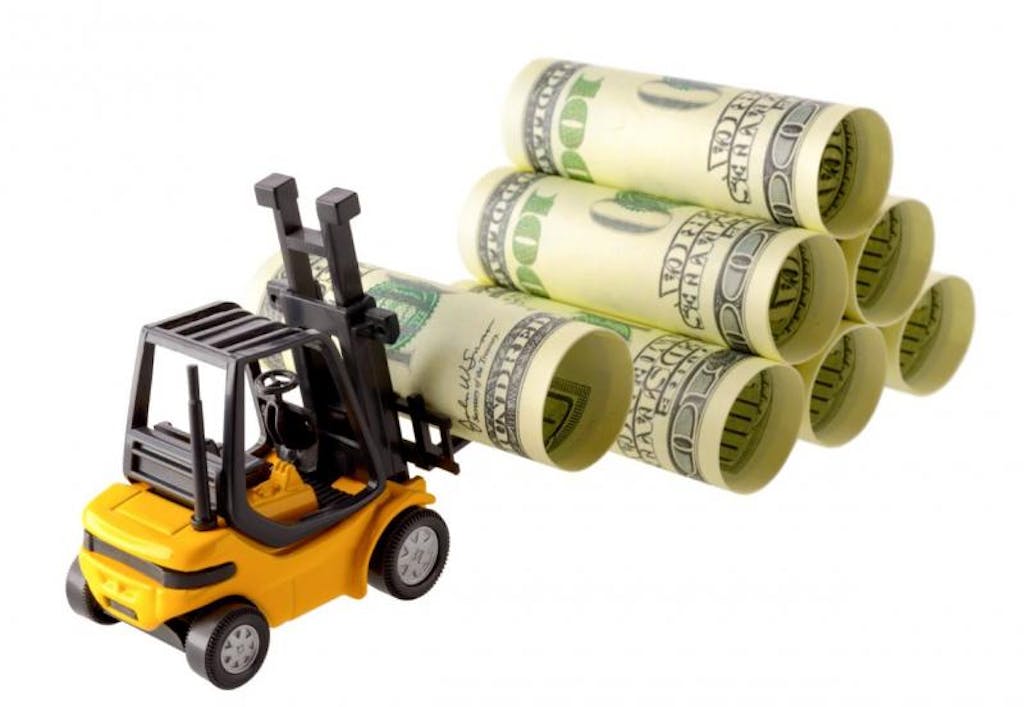
A forklift is an expensive piece of machinery, and in all cases, a lot of thought goes into deciding when to replace one after regular wear and tear. Of course, understanding the use and benefits of forklifts, as well as any safety hazards, is an important step. With the many safety hazards and costs in mind, companies are wondering when, if ever, they should make the switch to a forklift-free or forklift-reduced environment.
Benefits of Forklifts
Forklifts are very viable resources for indoor and outdoor activity and there are many benefits to utilizing forklifts. These include:
- Having easier access to an area which otherwise might not have been accessible,
- Being safer than step ladders, because they are more sturdy and allow workers to push/pull from a safe distance,
- Typically features a small truck that has a power-operated forked platform attached to the front,
- This fork can be inserted under cargo that needs to be more or lifted.
Safety Concerns
- Being crushed or pinched in the lift,
- Crashing into the warehouse racks or into other workers within the facility,
- The risk of causing electrocution to those using them if they are not insulated properly.
- The overturning of the forklift.
When using a forklift it is imperative that you first check the installation of the system as well as the machine itself to ensure that there is no damage so you can take preventative measures against possible injury. Those who are operating the forklift should check the surrounding area for any objects which might impede its vertical movement, and especially prior to moving the base of the forklift. There can be many obstacles to proper movement such as trees or power lines, the latter of which, if not checked for before movement, can cause electrocution and other serious injuries. There are large and small forklifts, each fit for different work. However, no matter the size, it is necessary that anyone who is operating the systems understand that all of the basic principles in the system work in the same way. There are some dangers associated with using forklifts.
The first is the possibility of getting crushed or pinched in the lift. The arms leave the possibility of having a limb or a smaller body part crushed underneath. To avoid this, hands and feet should never be placed under the platform or under the lift arms unless maintenance is being performed. If this is the case, then the machine should be turned off and the correct safety precautions should be taken before the machine is serviced to prevent injury. Forklifts run the risk of causing electrocution to those using them if they are not insulated properly. A forklift can conduct electricity which can severely injure the operator.
The lift should be placed far away from any hazardous environment. If there are power lines or an electrical apparatus nearby, those using the forklift should consider the possibility of swaying or movement while the lift is in use. Another possible safety hazard associated with forklifts is overturning. Overturning occurs when a forklift is thrown off balance and tips over. Overturning can cause serious injury and/or death. To avoid this, be sure not to exceed the weight limitations because the equipment might not hold larger loads. With an extended arm, a large load will leave the platform unbalanced as gravity pulls it down, resulting in overturning the entire apparatus. If the forklift is placed on uneven ground, then it could also overturn.
ROI Considerations for Replacement
With all that in mind, you have to be aware of the labor, safety, and integrity of the products. Given the aforementioned safety concerns, in fact, many companies are trying to move toward a forklift-free environment. After all, most of them are meant to move products vertically but they typically only move horizontally. Replacing them for something that provides horizontal and vertical reach can prove more cost-effective, productive, and efficient for the workplace. So, is it worth the cost to convert your company to a forklift-free or reduced environment, as part of the Lean or Just-In-Time initiative? Well, converting to a model like this does eliminate waste. It also gets rid of non-efficient processes, and of course, it removes any non-value-added activities. Systems that are properly designed will create instant process improvements especially when companies use battery-powered tuggers or tug. A tug can be operated without the need for special training. It can be hooked up to a cart (or multiple carts) after which it provides the muscle necessary to overcome the heavier loads, upwards of thousands of pounds (hundreds of kilos). Tuggers can move carts, trains of carts, and even dollies which means inventory can be kept low and aisles can be free from any excess products that would otherwise be lying around.
With traditional forklifts, there are larger space requirements, the forklifts have to be able to move down the aisles and around the workstations, and they need somewhere to be stored.
The power tuggers, by comparison, are compact and easy to move around. They just need a charge overnight and are ready to go.
There is also the risk of higher worker’s comp which can result in $50,000 in liabilities. On top of this, a fork truck can range anywhere from $15,000 – $30,000 (new). On top of this, there are the costs for the forklift driver, which needs special training and needs to be paid slightly more than regular warehouse workers. However, a power tugger will cost between $7,000 and $15,000 and doesn’t require special training for an operator to run. Based on your capabilities, a FlexQube cart will cost anywhere from $500 and this ranges depending on how many you need. There are factors to consider such as workers’ compensation claims associated with injuries, increased productivity, the cost and time for labor and training, the limited damage to pallets and products alike, and space requirements.
When your company looks at the costs of tugs and carts as a replacement for forklifts, in conjunction with a lean strategy, it should result in a positive ROI after the first year. At most, it would take up to 5 years, but that, again, is a worst-case scenario. So, when is the right time to make this change, if at all? Well, making it now would provide many benefits, especially when one considers replacing the forklifts with something else like a tug or cart. The benefits provided, the lack of special training and the reduced safety concerns are all something to take into consideration.
If you’re looking at reducing the number of fork trucks you have, contact us at sales@flexqube.com to learn how we can help.
You may also like:
Debunking the top 3 myths about tugger carts in material handling
How to start the transition from forklifts to a tugger train system