A smart factory is a flexible factory
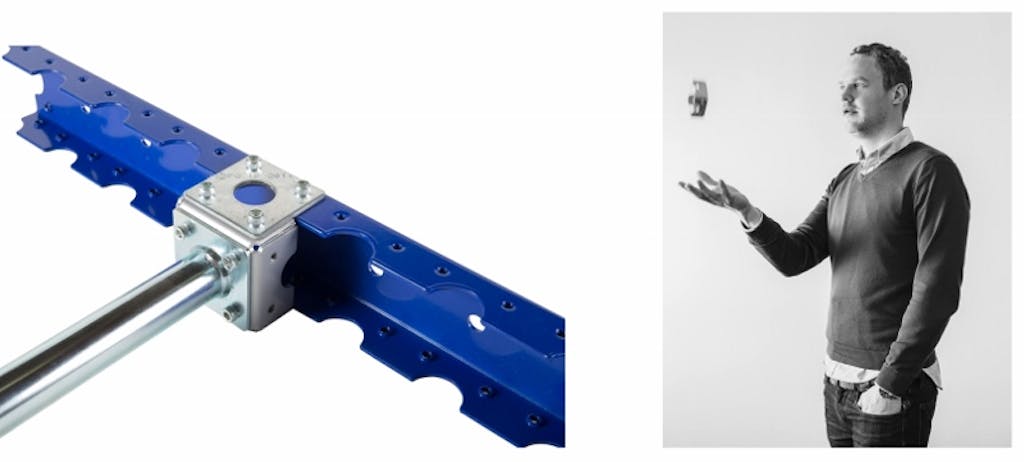
Last Modified: 21/04/2020
I’m a big fan of gadgets so I spend some time visiting electronics shops. Every time I do that I´m amazed about the huge number of products and variants that are available.
And every time they are a little bit cheaper and equipped with more features compared to last time. This trend is obvious for home appliance products. Different sizes, different colors, different types of technology, and a huge span in pricing level. And as this was not enough, most of the stuff is available on stock ready for pick up the same day!
Economist Ha-Joon Chang has claimed that the washing machine (taken as a proxy for all household technology), has been a more important invention than the internet (1). That makes sense. Nowadays worldwide shipments of household appliances exceed 580 million units annually and the forecast shows more than 700 million units by 2017(2).
As product life cycles gets shorter and shorter the need for flexible material handling equipment increases. At the same time the trend of fork lift free production areas also continues, which means that the demand for tugger trains and alternatives for line feeding with fork lifts is growing.
I think we all can agree that home appliance manufacturing is one of the most challenging and most competitive markets out there. Outsourcing of assembly to low-cost regions such as e.g. southeast Asia and eastern Europe is well known in the industry. The competition in the industry has forced the manufacturers to search for lower and lower wage structure. Many plants in Europe and the US have been closed over the years.
But now it seems like there is a change going on. Salaries have increased in low-cost countries, and in addition, products are getting more complex and stuffed with more technology. As a result of this, a growing number of US companies are reshoring manufacturing back to the United States. Producing products close to the market is good from a lead time and environmental perspective. And most important, it forces companies to make things in a smart way! Product design innovations in combination with state of the art factories can have a major impact on product cost.
Example
A good example is General Electric’s $800 million investment in jobs, products, and manufacturing processes in Louisville. In 2008, “lean” leader Rich Calvaruso gathered his team at Appliance Park and told them they had to rethink the dishwasher. He asked a team of factory workers, designers, and marketers to put their heads together. They managed to cut down the time it takes to build the dishwasher by one-third(3).
I´m sure we will see more of these initiatives. Close integration between design and manufacturing is the key to make things in a smart way. Smart factories will enable the production of ideas that the designers bring to the market, and smart product designs will enable that products can be produced in the most efficient way.
Want to stay up to date?
So, what is a smart factory?
I believe a smart factory is a flexible factory. A factory that can produce a variety of products and react to any type of change in an efficient way. Changed volumes, changing market requirements, improved regulations, and changed the political environment are just some examples. And looking back, we can conclude that change is the only constant.
A key enabler for a flexible plant is the industrial carts that transport material. The carts enable layouts and material flows to easily be changed. Carts are also a key enabler for implementing lean production as they enable parts and subassemblies to be presented in the best possible way for the operators. Overtime, when layout and products change, the carts also need to be modified in order to secure that operations are done in the most efficient way.
This is the basic idea of the FlexQube concept. They are enabling easy change by creating industrial carts with modular building blocks. Inspired by LEGO®, the blocks are combined into any customized solution. The carts can be designed by anyone using a web-based design tool, and the carts can easily be reconfigured when the needs are changing. Pallet carts, kit carts, tugger train carts, AGV carts. Anything is possible to create with the FlexQube concept!
-
Global