Mass Customization and the Factory of the Future
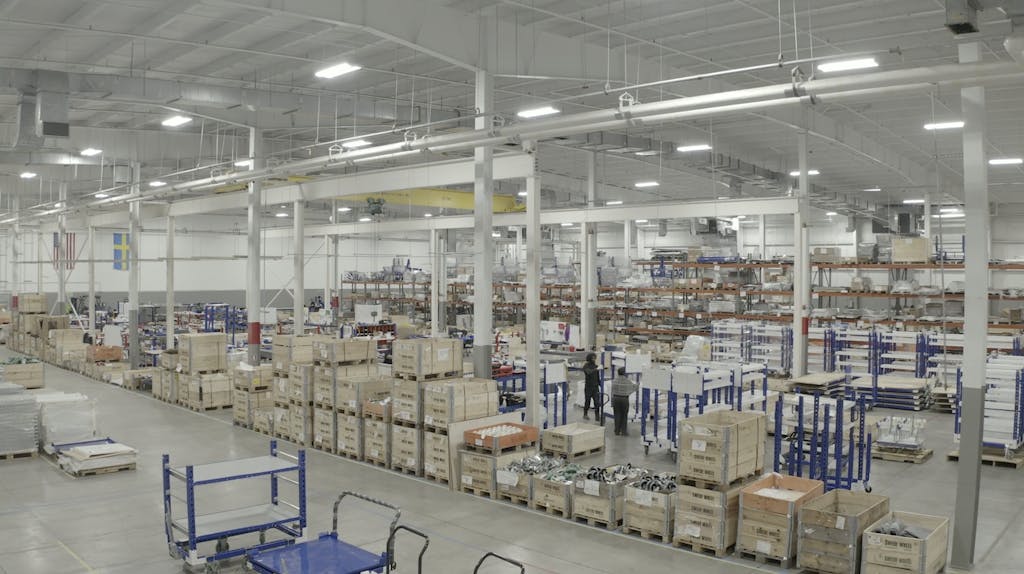
Increasing customer service levels is a sure way to gain the loyalty of customers.
Taking a leaf from the world of e-commerce, 74% of customers say they are likely to switch brands due to poor customer services. Customization provides the manufacturing industry with the opportunity to provide outstanding services to customers.
Customizing individual products tells the customer that you understand their desires and would do what’s required to meet them. However, focusing on the customer through customization to meet the needs of thousands of customers comes with operational challenges. To meet these operational challenges, the concept of mass customization was developed.
This post will discuss:
- What is mass customization and the business case for it
- The four faces of mass customization
- The role of digital transformation in transforming mass customization
- The role of mass customization in the factory of the future
What is Mass Customization?
Mass customization is the application of flexible manufacturing systems to produce customized throughput. The mass customization process involves capturing individual customer requirements and translates the requirements into the requested product.
Digital transformation technologies such as customization applications provide the interface customers utilize to put the features together into a customized product. Manufacturers can then take this information and turn it into the final customized product. The problem is traditional manufacturing facilities are generally designed to support discrete manufacturing processes not offer the flexibility customization requires.
Manufacturers who intend to provide mass customization on traditional manufacturing facilities generally end up questioning the process. This is because mass customization can lead to increased expenditure and complexities when executed using traditional manufacturing processes. With advancements in technology, the ability to develop flexible manufacturing facilities to cater to mass customization is possible. The flexible manufacturing environment will leverage digital transformation solutions and industrial automation to ensure mass customization can be done while leveraging lean concepts.
The Four Approaches to Mass Customization
Approaches to mass customization differ. The four popular approaches include collaborative customization, adaptive customization, cosmetic customization, and transparent customization. These four approaches define customer-manufacturer relationships and how they drive mass customization.
Collaborative Customization
The decision to offer customized services does not always come easy because in many cases, customers struggle with deciding on what exactly they want. To simplify the customization process, the manufacturer offers the listening ears of one of its technicians to the customer.
The customer in collaboration with a technician or designer then decides how the final product should look like before beginning the production process. Collaborative customization is a time-tested process within the manufacturing community. Manufacturers who offer customization services may provide a catalogue of the different components required to assemble the final product.
Applying the collaborative customization process to mass production means a more efficient collaborative system is required. Manufacturers usually do not have the resources to provide every customer with a representative. Thus, more efficient collaborative methods are required to deliver mass customization.
The challenges of collaborative customization include:
- Implementing a flexible manufacturing system to produce unique products in large quantities.
- Accommodating new workstations or shop floor equipment to deal with customer requests
- Providing diverse catalog or product options and features to thousands of customers interested in customized products
- Ensuring materials flow in order to meet increased demand for customized goods
- Reducing the cost of collaborative customization without affecting throughput quality.
Adaptive Customization
The adaptive customization process involves a manufacturer offering one product with diverse capabilities to customers. The customers can then choose to customize the product to meet specific needs. A simplistic example is the swizz knife. The knife comes in different configurations and customers who purchase the knife can adapt it to meet their specific requirements.
To deliver adaptive customization, manufacturers do not really have to change their manufacturing processes or rely on flexible manufacturing facilities. The manufacturing assets in place do the work of producing the manufactured good while the customer adapts the product or customizes the product as they choose.
The challenges of adaptive customization include:
- Ensuring customers use adapted products responsibly
- Producing product to meet the delivery deadlines customers expect
Cosmetic Customization
As advertised, cosmetic customization focuses on changing cosmetic features to provide customers with cosmetic differences. The manufacturer produces the same product but makes cosmetic changes such as changing the package of the product to meet individual customer specifications.
The cosmetic nature of these changes means the manufacturer does not have to modify aspects of its production processes to develop customized goods. With traditional manufacturing processes in place, the manufacturer can change packaging, the size of goods or other cosmetic features with ease.
The challenges of cosmetic customization include:
- Accommodating new workstations and machinery to support the customization process
- Managing the material handling process to ensure cosmetic changes do not increase production durations
- Developing customized products without going over specified budgets
Transparent Customization
The transparent customization process involves manufacturers providing customers with customized goods according to their needs. In this scenario, the customer does not make a request or may not even know they need a customized product. The manufacturer utilizes historical data from the customer to develop the customized good.
For transparent customization to work, the customer is usually a long-term user of the manufacturer’s product which gives the manufacturer the required data to work with. The manufacturer also may not have to make large-scale changes to deliver on transparent customization.
The challenges transparent customization faces:
- Capturing customer data to produce goods that provide answers to specific pain points
- Reducing the cost of producing customized goods that were not explicitly requested by customers
Transforming Mass Customization Process with Digital Transformation Solutions
Although the challenges manufacturers that adopt any of the four different types of mass customization face may differ, digital transformation solutions can be applied to optimize the production processes. Digital transformation refers to the application of technology solutions to transform business processes.
Manufacturers can leverage digital transformation solutions to solve the complex challenge attached to mass customization. To solve the problem of indecisive customers, the use of customization software or a digital design system can help. These software applications enable customers to choose features and add them to a product in real-time while testing how the finished product will look or function in the real world. The application of customization software ensures manufacturers do not have to hire multiple representatives to help customers decide on the features they want.
The application of customization or design software assists manufacturers interested in leveraging collaborative or cosmetic customization reduces the manual efforts and resources needed to customize goods. These applications capture customer requirements and digitally transfer these requirements to the manufacturer. The manufacturer then works with the captured data to produce customized goods.
Flexible manufacturing facilities are run on flexible systems. These systems include a flexible manufacturing layout, personnel flexibility, and flexible material handling process. Computer-aided design applications and simulation modeling software are digital transformation solutions that can be leveraged to develop optimized layouts.
An automated material handling system also delivers material transportation flexibility to meet the dynamic requirements of a manufacturing facility offering customization services. Autonomous mobile robots or automated guided vehicles can navigate shop floors without human assistance which enables just-in-time delivery to optimize productivity.
Manufacturers interested in offering transparent customization services can leverage data capturing and analytical solutions to determine the needs of their customers. The analyzed data can then be used to determine the customization assistance loyal customers require.
Mass Customization and the Factory of the Future
The lights-out factory of the future is one that thrives on the interexchange of data to reduce manual labor within manufacturing facilities. Industry 4.0 defines the factory of the future as one with fully automated processes. Thus, the process of capturing customized orders to fulfilling these orders is expected to be completely automated.
For example, within the context of collaborative customization, the customer inputs specific requirements on a design app which then transfers it to a manufacturing enterprise system (MES). The manufacturing enterprise system analyzes the customization requirements to determine the materials and resources needed to execute production. The MES provides this data to a simulation modeling and scheduling software that develops optimized schedules to determine when the product will be finished.
Data from the scheduling platform and inventory requirements from the MES is transferred to the autonomous material handling equipment which then picks up the required order and transports it to workstations. All these will be done without the intervention or need for human assistance.
To achieve the factory of the future will rely on advancements in data analysis, data transfer, and machine learning to deliver complete automation. Today, the OPC UA Foundation provides standards for the interexchange of data across the shop floor, autonomous mobile robots utilize machine learning to pick and transport materials, and automated robots can handle the manufacturing task…but a little human assistance is still required.
Humans still have the responsibility of updating robotic codes and monitoring manufacturing processes through remote monitoring solutions. The factory of the future intends to completely eliminate these human interventions to ensure mass customization happens smoothly with no unplanned downtime or human error.
Reach out to us!
-
U.S.