How to minimize downtime in your manufacturing after COVID-19
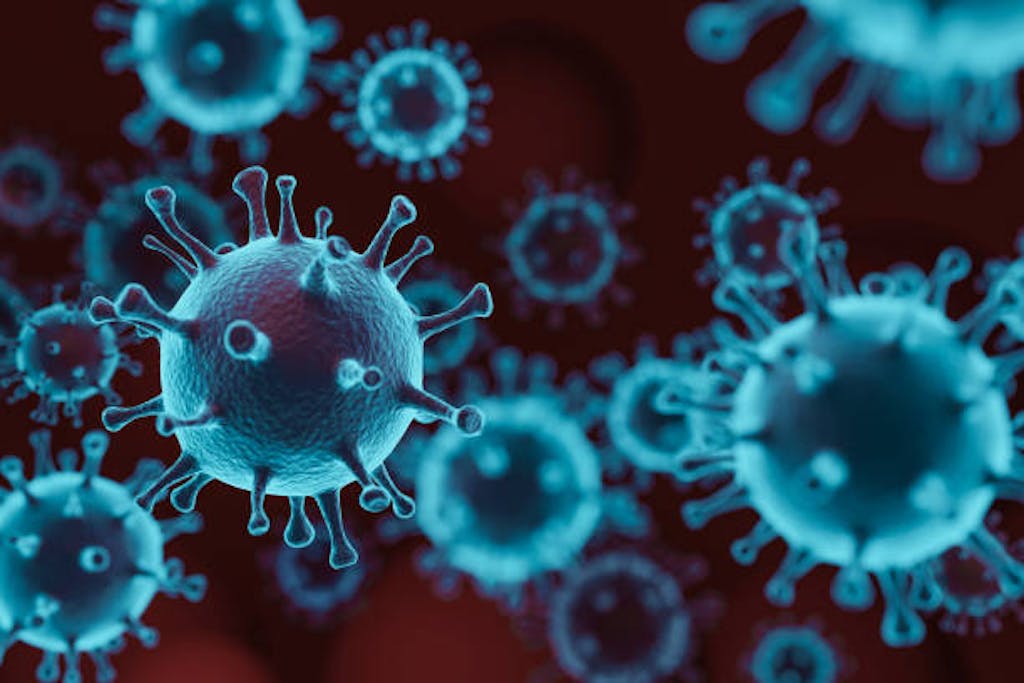
It’s safe to say that the impact of the COVID-19 pandemic on the world has changed how many will live their lives.
Everyone needs to begin a new set of rules for living life amongst others, including having social distance between people, frequent hand washing and wearing masks to prevent the spread. These new habits will become commonplace even after the impact of this virus is at its peak, and there will be a new set of habits that people involved in manufacturing will also have to learn.
The impact of the pandemic on the manufacturing world is broad and deep, impacting all areas. From the need to shut down plants during lockdown periods, to uncertain supplier timelines, and customer uncertainty. This all makes it difficult to predict how to open your manufacturing facility back up and what demand will be like once you do. There will be a few challenges for everyone when we look at how the future will look post COVID-19 and how we can expect to move forward, especially within manufacturing. Below we have outlined some challenges and some tips on how to overcome these challenges to minimize your downtime in your production after COVID-19.
Employee and Operator Safety
It’s evident that in a post-COVID-19 world that ensuring employees are safe and healthy will be one of the critical factors. Not only keeping your operators, engineers, and other assemblers safe and healthy is a duty of care as an employer, but it will also ensure limited downtime. Because as we have all learned it can be challenging to have a fully operational facility with people. But some steps can be taken to ensure you keep your operators safe and healthy. Firstly, you will need to create formal procedures within the facility and ensure everyone involved makes these new procedures a habit. Having set routines in place for different processes will be key to how successfully you are able to keep your employees safe. On top of this ensuring, solid communication between management and the operators on how to act during certain situations will create confidence throughout the workforce.
Secondly, you can ensure that people are not working closely with too many people. This enforces the now common place practice of social distancing. Leaving your operators to conduct their tasks in an area free from other operators has the benefit of social distancing and allowing them to focus on the task at hand.
Want to stay up to date? Subscribe below
Take Your First Steps into automation
Following on from keeping your employees safe and in an aim to reduce downtime if employees do get sick, taking your first steps into automation. Ensuring that you have some of your essential processes automated provides you with a buffer against labor shortages due to illness. You do not need to take huge steps with automation but taking some first few steps will ease the downtime if employees are unavailable. Our AGV is designed to provide a simple, affordable, and dedicated automation solution for manufacturing facilities. Ensuring that you can easily automate a few select processes within your facility is key.
Planning & Anticipating
Unfortunately, the effect of the pandemic has made it even more difficult for manufacturing facilities to plan the coming months. If it was difficult before this, it has almost become an impossible task now to predict and plan outcomes post COVID-19. So to combat this level of uncertainty we would encourage to increase the amount of scenario planning that needs to take place. You should outline more scenarios that may occur and make an action list in case one of these situations occurs. Some examples of situations you could begin planning for are:
- If an employee tests positive for COVID-19
- If you need to find substitute materials for your manufacturing
- In the case of a fall in the number of employees allowed within the facility
- Supplier goes into bankruptcy
- Can you produce hard to find materials yourself?
The above list is a simple list to begin working from, but the more scenarios that are planned for the more prepared you will be.
Embrace digital tools
Finally, we would recommend embracing a wide selection of digital tools that are available to manufacturers in the 21st century. If prior to the outbreak, your facility hadn’t tested using different solution now would be the time to begin. There is a vast amount of digital tools available to help reduce downtime in your facility, including:
- Track and Trace technology
- Augmented Reality
- Video Cameras and Filming
- Robotic technology
- Real-Time Data Collection
Beginning to become familiar with these technologies will begin to pay dividends for your manufacturing process in the future. It may lead to some headaches now, but it will also provide reduced downtime for your facility.
The impact of coronavirus has the chance to make an impact on society that is here to stay. Unfortunately, this means that the way manufacturing has been conducted will also change. While it may be difficult, especially in the next few months it is key to stay focused and be prepared for anything. So keeping a strong focus on ensuring your employees are safe, strong focus on planning and anticipating, and begin your first steps into automation and technology may make it easier for your facility in the future.