4 Steps to Integrating Six Sigma in Lean Manufacturing
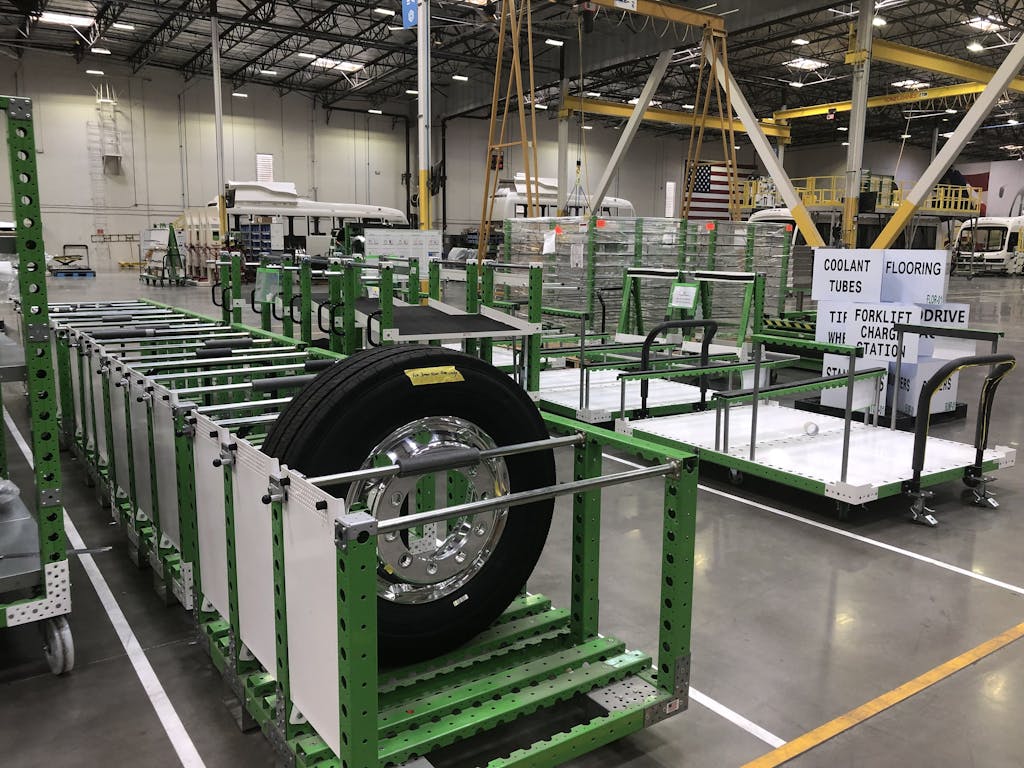
Every participant in manufacturing is always under constant pressure to reliably service demand without compromising on pressure and cost. This constant pressure has sometimes led to downtime and failure to meet demand. To eliminate downtime, the principles of Lean Six Sigma were created from the joint effort of Toyota and others.
The Lean Six Sigma process was developed with the aim of eliminating downtime, reducing waste while increasing efficiency in manufacturing. Here, we explore the four reasons to integrate Six Sigma principles in your lean manufacturing blueprint or activities.
Analyzing and Measuring Waste
The belief that the variables that cause wastage of time and resources can be measured is a cornerstone of Six Sigma. The first step to integrating Six Sigma in manufacturing is actually keeping records of the entire production process. To do this, an analytical software or tool is used to collect data such as customer demand, inventory, available tools, etc.
The mode of collaboration and transporting materials to meet these demands, as well as, the production process can also be assessed. The collected data can then be analyzed with the aim of stabilizing variables responsible for waste. In successfully completing the analysis, a lean model peculiar to that factory will be created. This model will serve as the stabilizing force for the production activities that will occur in the future.
Analyzing and Solving Transportation Issues
The process of handling materials, tools, or finished goods and transferring across a facility is one where waste also takes place. Poor material handling systems can slow down production as workstations may not be able to receive on-demand materials. Also, if the wrong or inadequate material handling equipment are used, this could lead to defects and reduced product quality.
So, the second step to integrating Six Sigma in lean manufacturing is getting the material handling and transporting process right. Here, options such as tugger train systems, and the option of customizing pallets, shelves, and containers will reduce extra processing waste, wait time waste or defects.
Analyzing and Eliminating Communication Challenges
To meet customer demand in a timely and adequate fashion, the communication channels in a manufacturing facility must function optimally. This is due to the fact that poor communication among, supply teams, and different departments will lead to downtime. The first step to dealing with communication and collaboration-related issues is analyzing the system in place. If it proves to be inefficient, changes in line with Six Sigma’s requirement for streamlined communication processes will need to be made.
Here, going digital may be the perfect solution to ease communication challenges due to the number of relationship and process management tools currently available. With the aid of a manufacturing system management tool, every party involved in the production process will be on one page. Certain processes, such as material handling, inventory keeping, and ticketing can also be automated to reduce. This reduces human error and the number of stakeholders participating in the production cycle.
Setting up A Comprehensive Lean Manufacturing Policy
Accomplishing the first three steps must be accompanied by getting everyone on the same page. To do this, extensive training is needed. Thus, every employee and even third-party suppliers must understand the companies corporate policy as it applies to lean manufacturing.
The road to integrating Six Sigma in lean manufacturing is made up of constant effort, vigilance, and regular application. Therefore, staff must be trained to apply lean manufacturing processes by rote.
Conclusion
At the core of Lean Six Sigma is the need to maximize the value you provide customers while minimizing waste. At FlexQube, our professional technicians can help you develop the material handling equipment or system required to eliminate waste.